Desarrollo local: Lanzadores satelitales con aluminio platense
El Laboratorio de Investigaciones de Metalurgia Física, de la Facultad de Ingeniería, obtuvo importantes avances en la fabricación y soldadura de aluminio para ser empleado en componentes que son utilizados para impulsar y viajar al espacio.
"Hace un tiempo, el decano Marcos Actis nos planteó la idea de trabajar sobre el desarrollo de aleaciones de aluminio de alta resistencia, con el objetivo de ser usado en la industria aeroespacial", recordó el ingeniero Alfredo González (foto), integrante del Laboratorio de Investigaciones de Metalurgia Física "lng. Gregorio Cusminsky" (LIMF), de la Facultad de Ingeniería de la UNLP.
Desde entonces, el LIMF ha obtenido importantes avances en la fabricación y soldadura de aluminio para ser empleado en componentes que son utilizados para impulsar y viajar al espacio. "Los dos primeros años del proyecto trabajamos, a escala de laboratorio, en el desarrollo de ese tipo de aleaciones y lo que son todos sus procesados mecánicos. Esto quiere decir que son aleaciones que tienen un tratamiento térmico que se complementa con un proceso de deformación plástica en frío para optimizar sus propiedades mecánicas.
Así obtuvimos una primera generación de aleaciones", comentó González a Ingeniar. En esta nueva etapa, se inicia la ampliación del proyecto originario. La propuesta del LIMF fue hacer un salto a escala semi industrial en el desarrollo de esas aleaciones. Para ello, el laboratorio interesó a una empresa nacional -con la cual venían trabajando desde hace un tiempo- que se dedica a la fabricación de aleaciones de cobre, la cual había adquirido un laminador y tiene la posibilidad de hacer chapa de un ancho de 300 mm; si bien se requeriría un ancho mayor éste resultaría un buen comienzo para la etapa semi industrial.
Con la empresa propietaria del laminador se alcanzó un acuerdo en el cual el LIMF le presta el asesoramiento para la puesta en funcionamiento del equipo y la empresa permite utilizar la máquina para fabricar chapas de 300 mm de ancho. Bajo esta forma de trabajo se ha avanzado en la puesta en funcionamiento del laminador, la cual estaría concluida en un par de meses.
Por otra parte, González mencionó que "estamos trabajando en una nueva generación de aleaciones de alta resistencia, hecha a base de aluminio-litio. Se ha avanzado en la búsqueda y análisis de la información disponible para este tipo de aleación, información que resulta relativamente poca dado que se trata de materiales estratégicos. A la fecha, estamos involucrados en lo que son los tratamientos de deformación plástica para llegar a una chapa de un espesor de 4 o 5 mm", explicó.
La chapa obtenida con este tipo de aleaciones se utiliza en la estructura de los tanques de combustibles que impulsa el lanzador satelital Tronador 11, desarrollado en nuestro país. Éstos "están fabricados con aleaciones de aluminio-litio y soldados con un proceso denominado friction stir welding, que nosotros también estamos desarrollando. Ese tipo de soldaduras permite la unión de chapas a tope, y otras configuraciones, mediante una soldadura en estado sólido. Nuestra idea es lograr fabricar chapas de 300 mm de ancho y soldarlas mediante este proceso y, de esta manera, poder ampliar ese ancho. Este proceso es uno de los más importantes y modernos en referencia a la unión de materiales", aseguró González.
Además, explico que "lo fundamental cuando uno quiere colocar un cohete en el espacio, es poner algo que sea lo más liviano y resistente posible, de manera que consuma la menor cantidad de energía posible para el impulso. Para ello, las aleaciones más livianas que tenemos son las de aluminio. Dentro de ellas, las más resistentes son la serie 2000, las aleaciones aluminiocobre, la serie 7000, que son aleaciones aluminio- zinc, y por encima de todas, están las aleaciones de aluminiolitio que son más livianas y más resistentes".
El ingeniero remarcó que uno de los principales problemas que tiene el aluminio en su etapa de fabricación es la absorción de hidrógeno. "Cuando la aleación pasa del estado líquido al sólido ese hidrógeno evoluciona, se separa del aluminio y forma una burbuja. Eso hay que evitarlo o controlarlo mediante un proceso de desgasiñcado y, para ello, hay diferentes acciones que se pueden aplicar".
Agregó que "trabajamos mucho en este tema y hemos alcanzado un importante conocimiento y desarrollo del proceso, lo que ha permitido contar con publicaciones tanto a nivel nacional como internacional y el asesoramiento de empresas del rubro, en el desgasiñcado de sus aleaciones a ñn de obtener una mejora en la calidad de sus productos".
Por último, González expresó que el objetivo del grupo de estudio de aleaciones no ferrosas del LIMF es "ver de qué manera los desarrollos de conocimiento que se generan puedan ser tomados y puestos en funcionamiento en una empresa, de manera que provoquen una mejora de calidad en su producto, que le permitirán el acceso a nuevos mercados, generando puestos de trabajos y divisas para nuestro país".
Publicada Originalmente en:
Revista Ingeniar Nro 4
Ficha: Alfredo Carlos González
Ingeniero Metalúrgico, Universidad Nacional de La Plata. "Doctor en Ingeniería, Universidad Nacional de La Plata.
Integrante del Laboratorio de Investigaciones de Metalurgia Física "lng. Gregario Cusminsky" (LIMF), Facultad de Ingeniería.
Profesor Titular Ordinario, Dedicación Exclusiva, Facultad de Ingeniería UNLP.
Director del Proyecto "Desarrollo de aleaciones de aluminio de alta resistencia para el uso aeroespacial", CONAE-Facultad de Ingeniería UNLP. 2010 a la fecha.
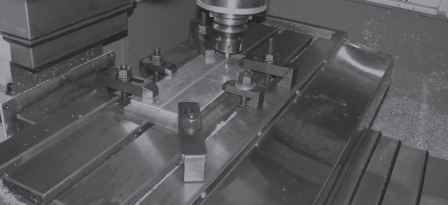
Dispositivo armado para la realización de la soldadura de dos chapas de aleación de aluminio de 5 mm de espesor.
Resultado de la soldadura de dos chapas de aleación de aluminio de 5 mm de espesor.
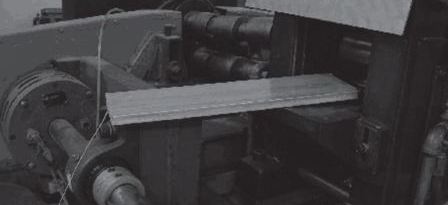
Fotografía del equipamiento utilizado para el proceso de deformación plástica por laminación.
.